Metal
seals are commonly used in aerospace applications due to their ability to
withstand extreme temperatures, pressures and harsh environments for critical
systems where elastomeric or polymer seals may not be suitable. Some typical aerospace applications for metal
seals include:
Aircraft Turbines, Satellites, Engines & Propulsion, Cryogenic Systems,
Oxygen systems, Rocket Liquid Fuel Tanks
What are Metal
Seals?
- Seals made of
special metals for static applications
- Particularly high elastic recovery
- For use in extreme operating conditions
Advantages of Metal Seals
- Temperature range from cryogenic (-270°C)
to 1000°C
- Pressures ranging from vacuum to 5000 bar, even at high temperatures
- Highly resistant to aggressive media - no shrinkage, no swelling
- No explosive decompression
- No aging by UV
light, ozone or oxygen
- Resistant to Radioactivity
- Pressure-activated
- Extremely low permeation/leakage (limited to contact areas between seal and groove)
- Lowest leakage rates:
Metal seals: up to 10⁻¹² mbar x Liter/sec per mm circumference = 1cm³ in 3000 years
Elastomer seals: up to 10⁻⁶ mbar x Liter/sec per mm circumference =
1cm³ in 2 weeks
Requirements for the Utilization of Metal
Seals
- Higher
compression forces
- Stable flanges
- Range of applications: static
Typical Applications
- Vehicle Exhaust Systems
- Fuel Injectors
- Aircraft Turbines
- Laser
- Oil and Gas Industry Equipment
- Gas and Steam Turbines
- Nuclear Applications
- Rocket Engines
- Satellites
- Turbochargers
- Vacuum
- Valves
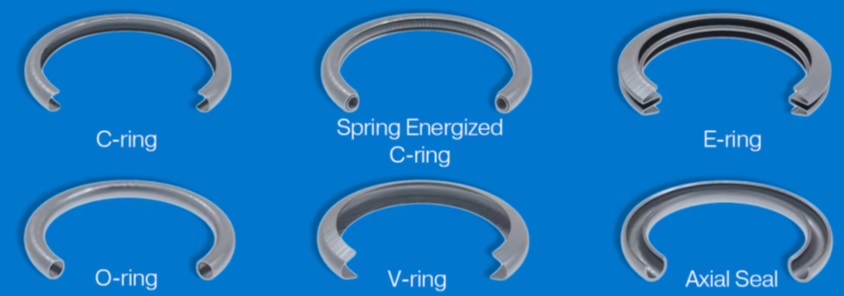